The team demonstrated exceptional flexibility, efficiently transitioning from conceptualization to the creation of manufacturable designs. The collaborative effort extended to engaging with factory contacts, ensuring seamless production processes.
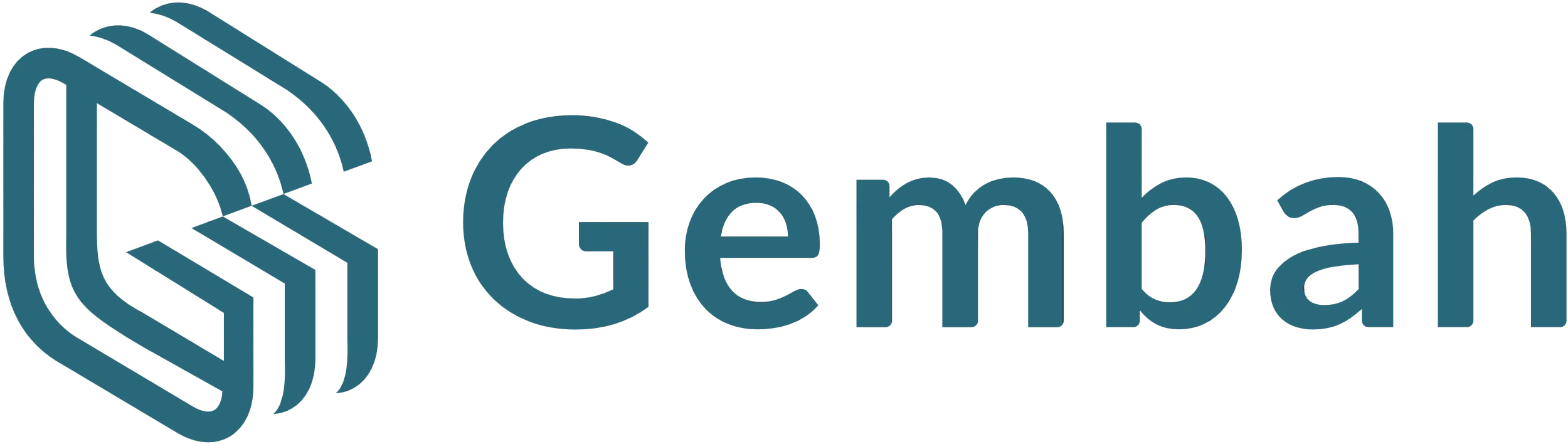
This Class II Medical Device was developed to pair with
Sedation Systems’ Nitrous Analgesia system. The product is
designed to safely remove exhalant and excess nitrous from the
environment by emptying it into a sink drain through the Vent
Connector. The product was designed to meet the FDA’s
requirements for scavenging, and fabrication and assembly was
sourced in the United States at an FDA approved facility.
Sedation Systems’ Nitrous Analgesia system allows doctors across
specialties to administer Nitrous Sedation for in-office procedures.
However, chronic exposure to Nitrous Oxide presents a risk to care
providers. To address this risk, Sedation Systems partnered with
Emergnt to develop a solution.
Latch Light’s original design, produced in collaboration with overseas factories, had several problems with it. Latch Light brough in Emergnt to address these issues.
The product had to meet the following criteria:
Our Mechanical Engineers analyzed an existing product, which Sedation Systems had been using for scavenging previously. Upon discerning that this product met the design requirements, our team reverse-engineered the device.
Our team developed 3D CAD Models of the new product. In this phase, off-the-shelf components like the internal pump and the fastening hardware were spec’d and modeled. Custom components, like the enclosure and the water trap, were designed to house and interface with the stock components.
Our Electrical Engineers designed the electrical and power system for operating the Miniscav. Our team analyzed the previous design to ensure that it met the safety standards outlined in the requirements. Then they spec’d off the shelf components and hardware and created a wiring schematic for production partners to follow during assembly.
Following a design review with Sedation Systems and their approval, our engineers drafted Production Drawings based on the 3D CAD Models. These files detailed the Product & Manufacturing Information (PMI) and would be the primary reference for production. The files included dimensioned drawings, flat patterns, an assembly drawing, and a BOM.
With these files, our team Sourced Production for the device. In accordance with the requirements, our team engaged with multiple FDA-approved facilities. We coordinated with Sedation Systems’ FDA consultant on the other regulatory requirements for the production facility.