The team demonstrated exceptional flexibility, efficiently transitioning from conceptualization to the creation of manufacturable designs. The collaborative effort extended to engaging with factory contacts, ensuring seamless production processes.
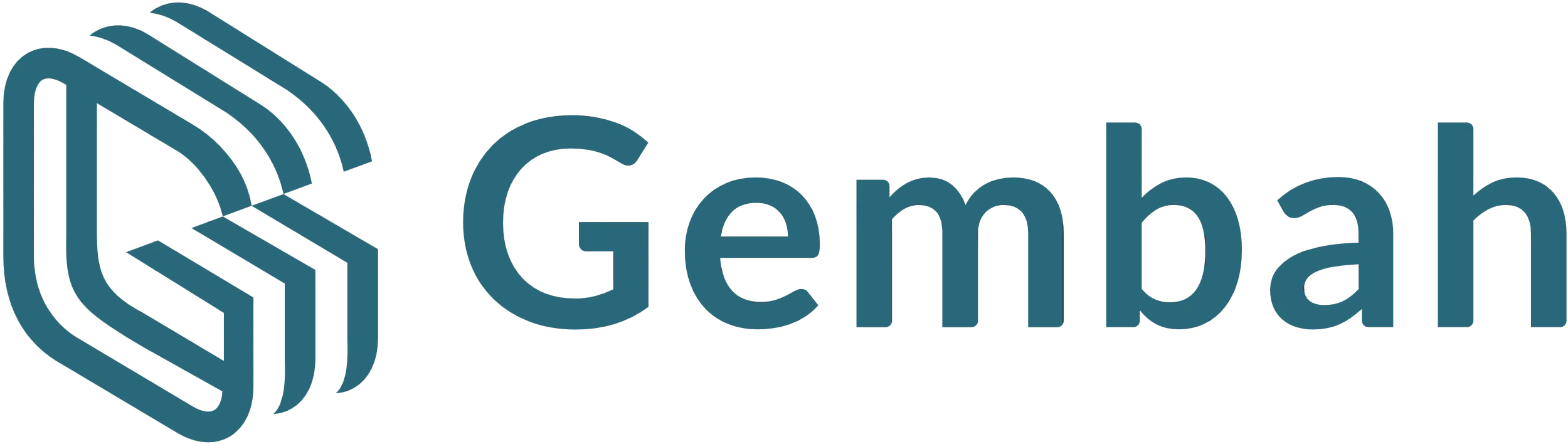
This piece of production equipment, developed through a partnership with Northern Illinois University, is designed specifically for the Large Hadron Collider. Our engineers modified existing 3D CAD Models of the equipment to the specs provided by NIU and drafted Production Drawings for CNC Machining.
Emergnt was contacted by an engineering research professor at the University of Illinois whose group was collaborating with CERN in designing portions the Large Hadron Collider near Geneva, Switzerland- a piece of particle physics research equipment which happens to be the largest machine in the world. The group was developing production equipment for a portion of the Collider- a cavity lined with tens of thousands of photosensitive "tiles". Prior to installation, the tiles needed to be stored in a specialized "wrapper" for protection. Thus, the NIU team had designed a custom Production Punch- a piece of machinery used to punch out the wrappers in the appropriate shape.
NIU sought the help of the expert CAD designers at Emergnt to modify the existing CAD models of the machinery and produce new, up-to-date production drawings. Among other design modifications, the NIU group wanted to change the geometry of the punched wrappers. They provided our team with a series of profiles- the shapes that the device must punch wrapper material into.
Our Mechanical Engineers analyzed the preexisting design CAD files to understand mechanics of the device before modifications were made. They determined that the punch's central arm must align with the geometric centroid of the wrapper profile for proper function.
Armed with this information, our team modified the 3D CAD Models to the specs provided by NIU. Our professionally-certified designers were able to interpret and preserve the design history left by the previous designers without needing to start from scratch.
With the design modifications approved by NIU researchers, our team drafted a new set of Production Drawings. These files detailed the custom parts in the assembly for CNC machining and included ordinate dimensions, surface finishes, and tolerances.
Emergnt worked with the NIU team's schedule as college instructors, conducting virtual design reviews at their convenience. With the project complete, the group expressed their satisfaction with the results and their experience working with Emergnt. The project was a great example of how our On-Demand team can collaborate with other engineering & research groups on small tasks to help them more efficiently accomplish larger goals.